Pinnacle Custom Signs was fortunate enough to be the selected sign provider in 2018 for several of the Fulton County Library Systems renovation efforts.
The award included the overhaul of 21 different branch’s monument signage for the Fulton County Library System to enhance the branding consistency.
Pinnacle is working with the AFLPS’s Wayfinding Consultant, EPY/Stanley Beaman & Sears, to fabricate and install standard monument signage for each location.
Each sign has been customized to fit each library’s topography and building material façades such as similar masonry and roof materials.
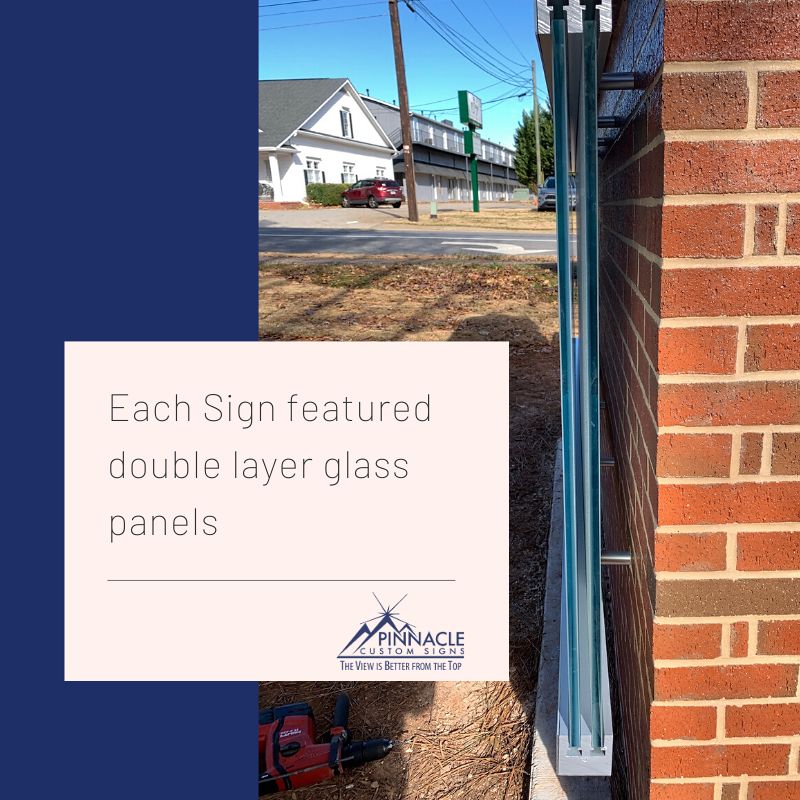
The Design Process
The beginning of this project included figuring out how to construct the signs to give the Fulton Public Library System the best impact and appearance for each sign.
The design of the monuments called for having a lighted panel behind glass panel sign face that would be mounted to masonry monument signs.
The first challenge was creating the process behind the double layer glass panels.
The front glass was constructed of ½ inch Star Fire glass that needed to be frosted and then painted with the specific location information for the library. These details included the library name and the address and the FCLS logo.
The back-glass panel featured also featured ½ inch Star Fire Glass, but this panel featured a hex engraved pattern that Pinnacle produced in house on our new glass engraving machine. Our team actually purchased new engraving equipment specifically to ensure that we could provide the FCLS with the quality and pattern that they desired.
In order to install the two glass panels securely, an aluminum channel with two tracks was secured to the masonry monument signage. The channels featured drilled ports for wiring the lights that would illuminate the glass panels. Additional drilled holes were used to install the glass panels with studs on the masonry and secured with Hilti Epoxy. Then we installed aluminum covers to hide the screws in the extrusions for a clean look.
Challenge #1 – Sign Installation
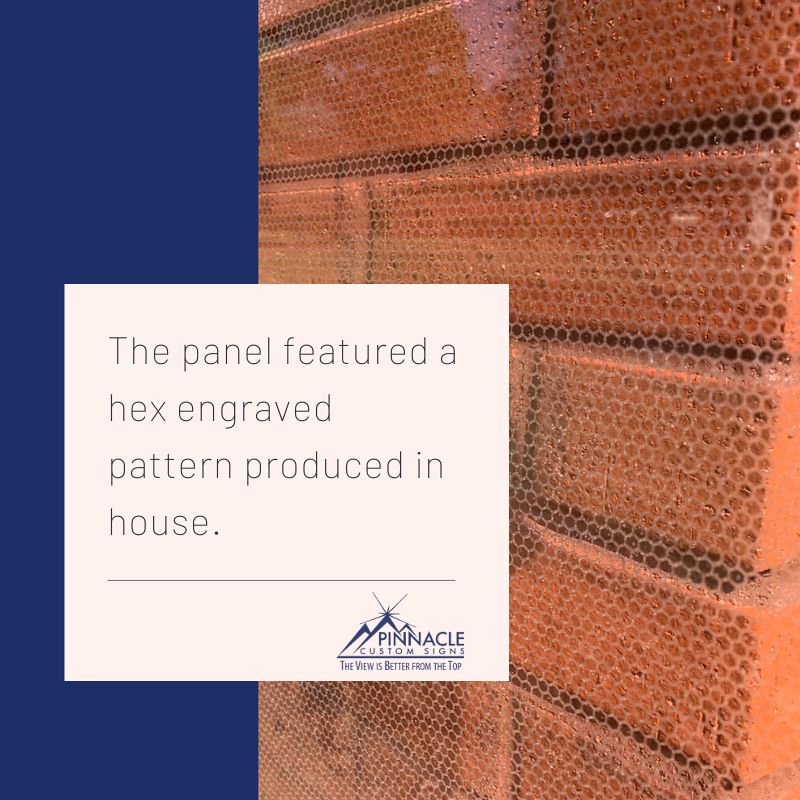
To say that the installation of these signs was initially challenging is an understatement. There are several elements to creating these signs that were not common for our team.
First off, we needed to find a turnkey mason who had the capacity to provide high-quality masonry services for several locations over a long duration. Pinnacle wanted to make sure that we got consistent quality for the brick monument panel since the signage for each location was not going to be installed simultaneously. This was more of a challenge then we were expecting.
If you ask anyone in the construction industry who deals with trade contractors, they would tell you that everyone is so busy that they are backed up for months with work. The masons who do a good job are hard to find and busy on larger projects. Most of the masons we normally use were either booked with work or this project was beyond their scope of capabilities.
Luckily for our team, we have a database of clients in numerous industries – including construction. So, we did what we constantly ask for others to do for us – give us referrals!
We reached out to a couple different clients who gave us the name and numbers of local masons who they knew could perform this task and wished us the best of luck getting them to fit it into their schedules. Don Conklin got on the phone and started reaching out to find a mason who would be willing to commit to helping us across Fulton. With a little networking, he secured a great source to build out or rebuild the masonry for the 21 locations.
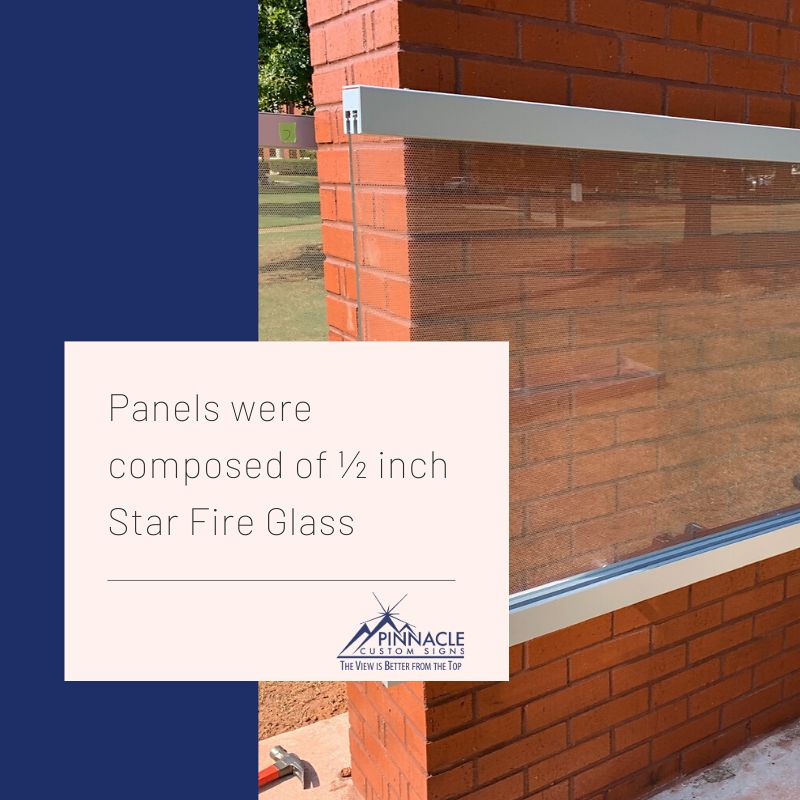
Challenge #2 – Ensuring Quality and Timing
When we began this project, we factored in having close to 95% of the production of the different materials outsourced. That included the masonry walls, hex pattern Star Fire Glass, wiring for the lighting illumination systems, and aluminum channels used to house the glass panels.
Due to quality concerns and the ability to turn the project around in a timely manner, Pinnacle stepped up to bring the production of most of the elements in-house.
Instead of looking for a third-party source to create the custom patterns for the glass panels, we invested in the next generation of machinery to help us custom produce the hex pattern. Then we used our own in-house expertise to both frost and paint the front panels.
Our installation experts went out on-site to examine the final construction of the masonry walls and the exact location of the ½ inch gap opening that is located within the structure.
We had to ensure that when we drilled in the studs to hold the channels that we didn’t drill through the entire structure. If the studs were drilled all the way through the wall they would hit air pockets that prevented the Hilti epoxy from drying appropriately.
So, creating specific instructions and ensuring stud depth was a critical component of this process. Then our crew handled pulling the wiring through the aluminum channels and securing the lighting for the final effect.
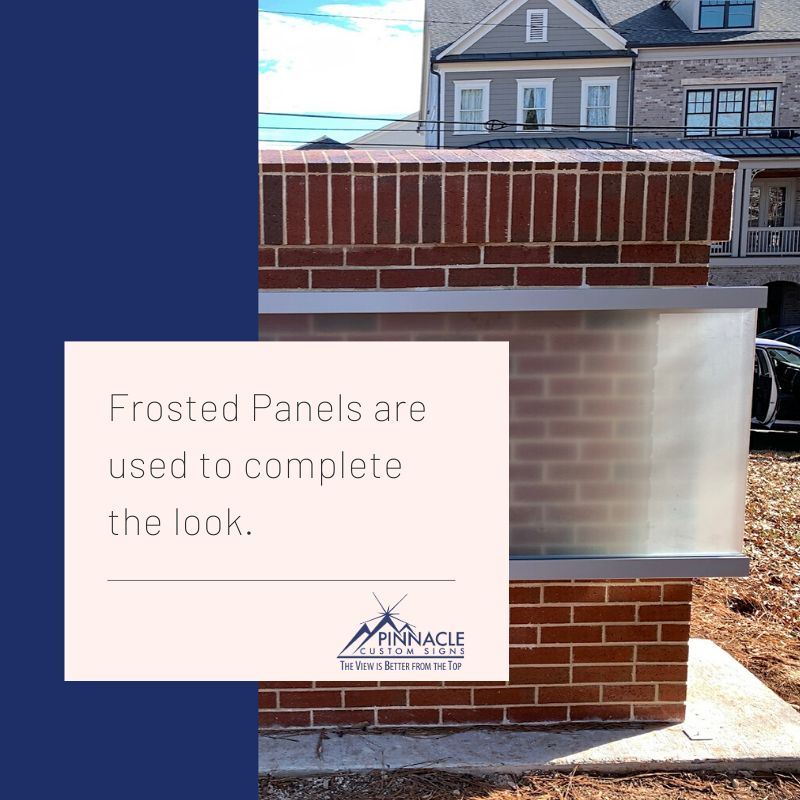
Finding the Right Process
Our team has now completed ten of the twenty locations for the FPLS. New signs can now be seen at the Roswell, Dogwood, Kirkwood, Washington Park, West End, East Point, College Park, Adams Park, Cascade Park, and Fairburn location.
Through this process, we have learned a lot about the capabilities of our team to overcome unforeseen challenges and connect with the right referral partners to get a project done for the owner. We have also been able to rise to the challenge of creating a custom look for a public client who needs their project done on budget and within time.
We are ready to meet the challenges of all our clients and figure out the best solutions for architecturally designed projects to match the design elements of the building and spaces. Our firm regularly holds meetings with all parties on-site to ensure quality procedures and quality inspections to ensure our clients are getting the very best for their value. Give a call for a free consultation about your property’s needs or specific signage issues.