Over the last 9 years, Pinnacle Custom Signs has grown to be the signage solution experts our clients can depend on for all their needs. Our team has focused on being a local and national customer service provider — not a just a sign company.
However, our customer-focused capabilities changed during the 2019 so that we can provide better solutions for our clients.
We have always produced any signage our customers need for their business, from as small as vehicle graphic to full-scale building and monument signage.
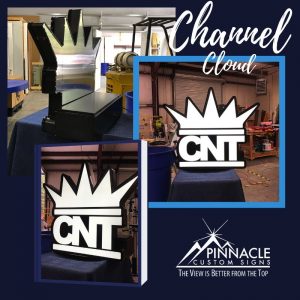
Up until late 2019, all print production such as graphics were produced in our shop in Buford, GA. This allowed Pinnacle to focus on providing customers with quick print delivery and produce signs with very short timelines.
Our team has always been able to do this by using the four printers, a laminator and two in house cutters to produce signage needs from flat signs to vehicle wraps.
When we needed to produce building signs and lighted signs for a client, since we opened our doors, we have maintained an excellent relationship with our outsource vendor to provide competitive pricing as well as meet many deadlines.
However, this past year, we realized our production capabilities needed to ramp up to meet the demand of the ever-growing sign market.
New Sign Fabrication Machines = Faster Sign Turnaround
After researching bringing on additional in-house production capabilities, our management team decided that adding sign fabrication capabilities in-house would help us be able to provide better service to our customers.
So in December of 2019, Pinnacle purchased a handful of new machines including:
- Channel Bender
- 10’ Break
- 4’ by 8’ laser router and engraver
- Along with numerous smaller tools of the trade
Pinnacle can now produce Channel Letters, Lighted Cabinets, and Custom Fabricated signs in-house to provide better response times.
Channel Bender
The new channel letter bending machine allows us to create Channel Letter Signs in-house.
An aluminum coil is fed into the machine. The machine takes the coils, using a computer-guided program, the coil is notched and then a flange (or lip) is bent on the aluminum to allow it to be attached to the back of the letter.
Once the coil has been notched and flange added, the letter is bent using the metal arm to form a smooth letter.
After the coil comes from the Channel Bender, our fabrication team goes to work. The letter is formed and riveted together. Then the back and front of the letters are routed to make the letter rigid.
The back of the letters are routed from 3mm (1/8”/.125”) Aluminum Composite Material. This back piece will then get LED lights to illuminate the letter.
The face is routed out of Acrylic and trim cap is added to allow the face to be attached to the body of the letter. This will diffuse the light and provide the finished look of the letter.
Channel Letters can be individually mounted, or raceway mounted.
When individually mounted, the individual letters are mounted directly to the building, one at a time.
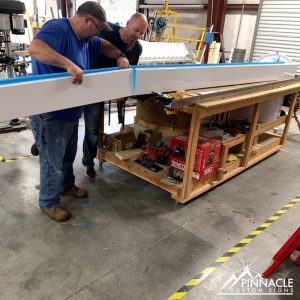
Raceway mounted signs are mounted to an aluminum structure called the “Raceway” and then the entire sign is installed on the wall in one piece.
In order to construct a “raceway”, the team starts with .040 aluminum sheets. The sheets are cut to size and taken to the Break to be formed.
The Break
The Break allows the sheets to be bent to shape, making 90º bends accurately. After the “raceway” is formed, the team adds structure to the interior to allow for mounting and support.
Once the entire raceway is complete, the team makes a pattern to put the letters on straight, spaced correctly, and accurate. The team then through bolts the letters to the raceway.
Another capability of the Break is to produce lighted cabinets, like this one for Perfume World.
In order to achieve this, the team starts with the correct thickness of aluminum sheet material to support the cabinet. The thickness for smaller cabinets maybe .040, and larger cabinets can range from .080 to .125” aluminum.
The team designs a routing file for the shape, allowing for accurate bends and positioning for fastening. The ends are bent around each other in the corners and riveted together to form the structure.
Once the “shell” of the cabinet is built the team then goes to work on the interior to provide support and structure. The team used .125 flat bar aluminum, as well as .080 sheet aluminum to increase the rigidity of the cabinet holding the face.
After all these pieces are assembled, the cabinet gets LEDs and a face to complete the product before it is ready to be installed.
What that Means to You
With all of these capabilities brought in house, we are able to produce signs quickly and accurately in order to meet the needs of all of our customers. Along with the ability to produce letters in house, we have been UL certified. This allows us to ensure our lighted signs meet all requirements in all jurisdictions nationwide.
If you are looking for a new signage provider or have a project you would like to discuss, please feel free to give us a call.
Our team is ready to find the right solutions for your signage needs. We have dedicated professionals standing by to provide answers questions for you at no charge. We look forward to using our new capabilities to help you find your next customers.